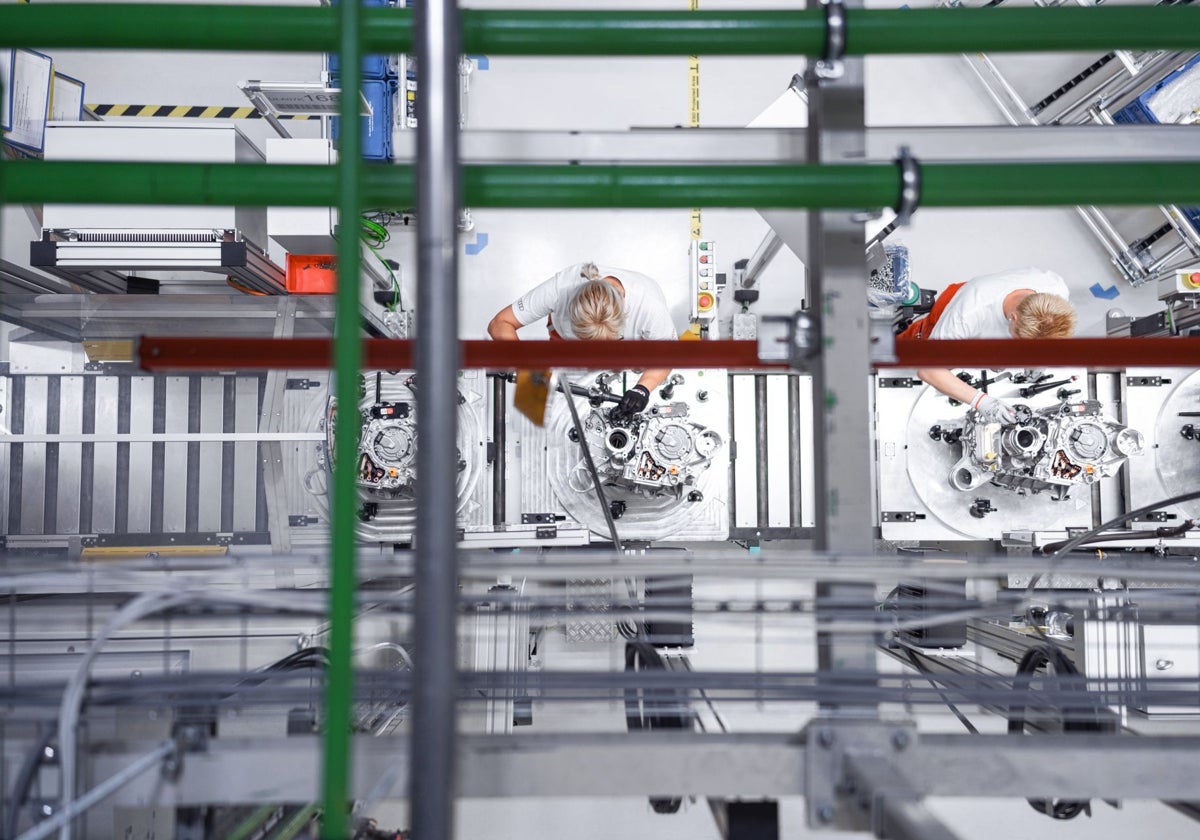
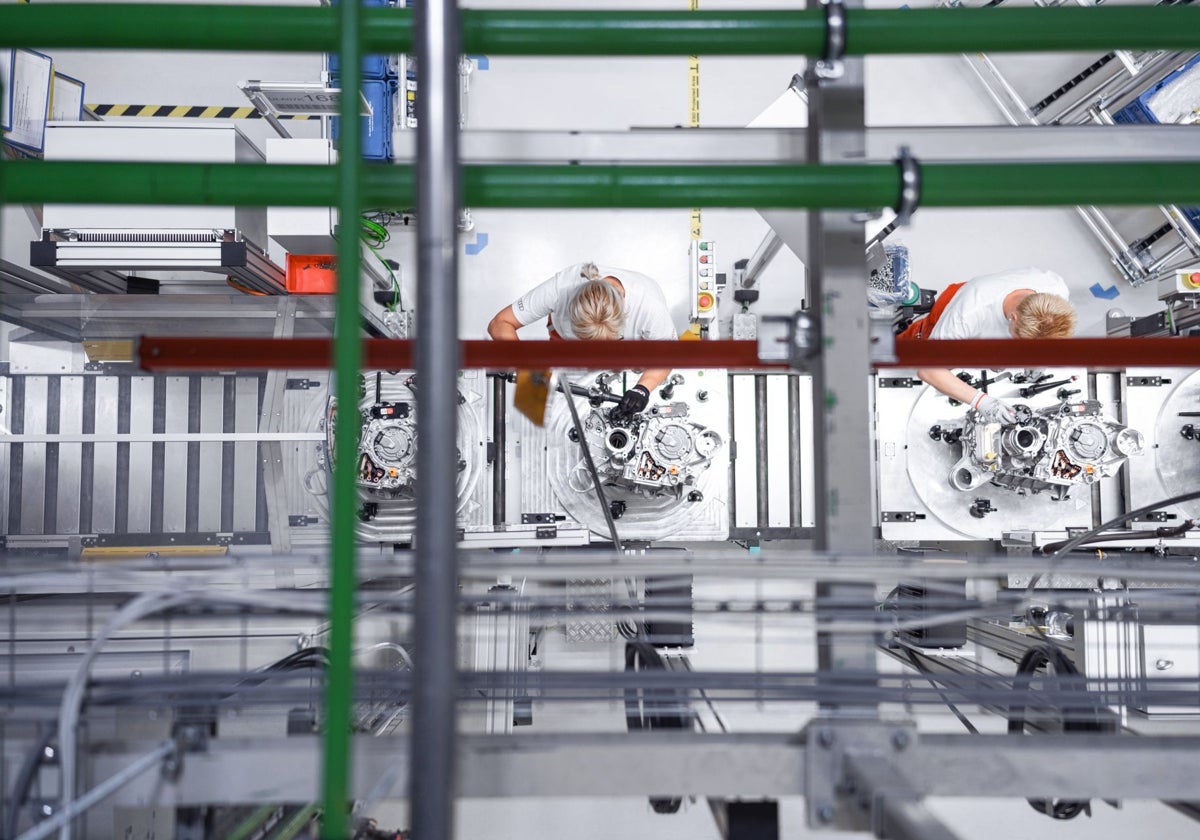
Secciones
Servicios
Destacamos
José Ramón Alonso Trigueros
Viernes, 10 de enero 2025, 08:52
El desafío lanzado desde las instituciones europeas para reducir las emisiones llevó a la industria automovilística a aplicarse en la búsqueda de tecnologías que sustituyen al tradicional motor de combustión. En esa pelea contra el reloj, la mayoría de las empresas apostaron por la electrificación ... como respuesta para sus nuevos modelos. Hoy en día, la mayoría de las compañías tienen en su catálogo vehículos electrificados.
Ahora llega el nuevo reto para los fabricantes, que es conseguir que el proceso de ensamblaje se realice en factorías ecológicas, donde se preste una especial atención al ahorro energético en la búsqueda de que todo el proceso sea tendente a las cero emisiones.
Para ello, lo primero que han hecho es buscar fuentes de energía verdes para dar respuesta a las necesidades de producción. Aquí aparecen en la mayoría de las plantas de producción automovilística grandes campos de paneles solares –despecialmente en las azoteas de las naves–, molinos de viento para aprovechar la fuerza eólica y otras formas de generar energía limpia.
Un ejemplo de adaptación para conseguir fábricas neutra en emisiones es la planta de Audi en la localidad húngara de Györ, que desde 2013, coincidiendo con el arranque de la fabricación de automóviles, pone en marcha el centro de energía G42 que ha llevado a que desde 2020 la planta de húngara de Györ sea neutra en emisiones de CO2. Para ello se ha trabajado especialmente en dos vías. La primera fue la instalación de un sistema de calefacción a través de energía geotérmica y la otra fue la instalación en 2020 de placas solares en los tejados de algunas de las naves de la fábrica.
En 2016 Audi Hungría firma un contrato con una empresa para el suministro de energía geotérmica, que geolocalizó a 15 kilómetros de la planta una bolsa de aguas termal que aporta el 92% de la energía para la calefacción en un país que en invierno puede tener temperaturas por debajo de los -25 grados.
La extracción de energía geotérmica se hace mediante la perforación a 2.500 metros de profundidad desde donde bombean el agua caliente que está a casi 100 grados centígrados. Después de su uso se reintegra el agua de nuevo en el acuífero termal. El agua se devuelve cinco kilómetros más allá del lugar extraído y tardará 5 años en volver a coger la temperatura inicial. La de la fábrica de Györ es la segunda estación geotérmica más grande de Hungría.
El ahorro en un año puede equivaler a 100.000 megavatios de energía y es más del 50% de energía que consume la planta.
En 2020 se firma contrato con empresa eléctrica en la que se construyó la superficie de placas solares más grande de Europa, con 160.000 metros cuadrados que equivale a 22 campos de fútbol.
Esta factoría comenzó su andadura hace 26 años con la fabricación del Audi TT. Hoy, de sus instalaciones, con 5.142.115 metros cuadrados y 11.663 empleados, salen casi 180.000 (177.775 en 2023) de los modelos Audi Q3, Audi Q3 Sportback y de los modelos Audi TT.
Pero más allá del montaje de vehículos, lo que sitúa de forma destacada a Györ en el ecosistema de Audi es su producción de motores, que fabrica sistemas de propulsión para el Grupo Volkswagen desde 1994. Con los años, la empresa se ha convertido en la mayor factoría de sistemas de propulsión del mundo. En 2023, Audi Hungría fabricó en Győr 1.660.425 motores para 35 centros de producción del Grupo Volkswagen.
De los motores fabricados en 2023, 1.164.289 eran de gasolina y diésel de tres y cuatro cilindros. Los empleados de la planta produjeron también 19.734 motores de gasolina de cinco cilindros, 277.081 motores de gasolina de seis cilindros, 78.905 motores diésel de seis cilindros y 6.216 motores de diez cilindros. Además, en Györ se fabricaron 114.058 sistemas de propulsión eléctrica.
En total, Audi Hungría fabricó seis variantes diferentes de motores de gasolina y dos diésel en 2023, así como dos familias de motores eléctricos, con un rango de potencia de 90 kW (122 CV) a 180 kW (244 CV).
Los motores eléctricos se producen en Györ desde 2018. En los años transcurridos, su cuota en el volumen total de producción ha aumentado considerablemente. Los motores eléctricos que se fabrican en este emplazamiento se utilizan en el Audi Q8 e-tron, el Audi Q6 e-tron y el Porsche Macan. Los nuevos sistemas de propulsión para los modelos totalmente eléctricos del Grupo basados en la Plataforma Premium Eléctrica (PPE) también serán suministrados por Györ. Para su fabricación, en 2022 se acondicionó una nueva zona en la factoría.
También se está preparando una zona adicional para fabricar los nuevos motores para la plataforma MEBeco. Audi Hungría producirá entonces una nueva familia de motores eléctricos con una mayor integración vertical.
Por ejemplo, por primera vez se fabricará en serie el paquete de laminado metálico que conforma el núcleo del motor eléctrico. En el futuro también se fabricarán los rotores y la electrónica de potencia. Estos sistemas de propulsión se emplearán posteriormente en los vehículos eléctricos pequeños del Grupo Volkswagen.
· FUNDACIÓN Comenzó su andadura en 1993 con la fabricación del Audi TT. Hoy salen casi 180.000 vehículos de la cadena
· EMPLEO Da trabajo a cerca de 12.000 empleados que trabajan en una instalación que ocupa 5.142.115 metros cuadrados
· MODELOS En la actualidad, la empresa produce el Audi Q3 y el Q3 Sportback. Su debut en 1998 fue con el montaje del Audi TT
Audi fabrica los motores eléctricos para la Premium Platform Electric (PPE) en la planta de propulsión más grande del mundo en Györ, Hungría con una superficie de unos 15.000 metros cuadrados, además de producir componentes del estator y la transmisión y ensamblar los ejes. La línea de producción de estatores tiene 28 pasos de trabajo, la de componentes de transmisión tiene 15.
El montaje de un eje requiere más de 190 pasos individuales. En total, en la producción de los sistemas de propulsión de los EPI trabajan unos 700 trabajadores. En Györ, tres turnos permiten producir en serie 2.000 motores eléctricos para los EPI cada día. Los sistemas de propulsión eléctricos que fabricamos aquí son para los modelos de EPI de Audi y Porsche.
Los empleados necesitaron 20 días de formación cada uno para aprender todo. Llevan fabricados más de 500.000 motores eléctricos desde 2018. Solo para el PPE utilizan 15 máquinas dobladoras automáticas para hacer los bobinados tridimensionales en forma de horquilla y dos sistemas para soldar con láser los extremos a continuación. Cada estator contiene 140 metros de cable de cobre.
Se necesitan un total de 235 soldaduras láser para fabricar uno. En comparación con los modelos de motor de combustión, los eléctricos suelen tener menos fijaciones atornilladas, pero requieren más prensado, por lo que se pueden utilizar más robots.
Publicidad
Publicidad
Te puede interesar
Publicidad
Publicidad
Esta funcionalidad es exclusiva para suscriptores.
Reporta un error en esta noticia
Comentar es una ventaja exclusiva para registrados
¿Ya eres registrado?
Inicia sesiónNecesitas ser suscriptor para poder votar.